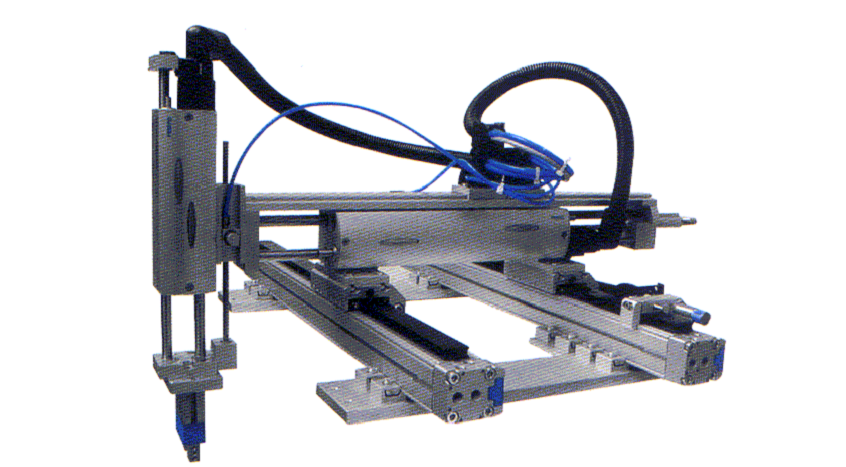
Khí cụ chẩn đoán sự cố
Chẩn đoán sự cố điện thường dựa trên các đo điện áp, cường độ dòng điện trở (ít dùng hơn) tại các điểm then chốt trong mạch. Trong đó, điện áp dễ đo hơn dòng điện trừ khi sử dụng ampere kế, đo điện trở thường yêu cầu ngắt mạch nguồn. Mạch điện tử được minh họa trên hình dưới đây chuyển điện áp ngõ vào Vi thành tín hiệu dòng I, với I=Vi/R. Loại mạch này thường được dùng để truyền tín hiệu đo qua môi trường có nhiễu. Quy trình kiểm tra bao gồm:
- Đo điện áp: A tín hiệu ngõ vào
- B và C (nguồn +- của bộ khuếch đại)
- D (Điện áp trả về phải bằng A)
- E (qua tải, 15V nghĩa là tải ngắn mạch, 0V nghĩa là tải ngắn mạch).
- Đo dòng điện: X, Y (X nên bằng Y và cả hai đều bằng A/R)
- Đo điện trở: F, G (mạch điện bị hở hoặc ngắn mạch, hoặc điện trở)
Trong hệ thống thủy lực và khí nén, đo áp suất tương đương với đo điện áp, đo lưu lượng tương đương với đo dòng điện. Không có phương pháp đo đơn giản trực tiếp tương đương với điện trở. Kiểm tra áp suất và lưu lượng là cơ sở để chẩn đoán sự cố trong hệ thống thủy lực/ khí nén.
Tuy nhiên có sự khác biệt cơ bản về phương pháp tiếp cận. Hệ thống điện có nhiều điểm kiểm tra điện áp, có thể đặt bộ dò điện áp vào vị trí hoặc bộ phận bất kì trong mạch điện, và có thể tạm ngắt mạch để đo cường độ dòng điện.
Trong hệ thống lưu chất thủy lực, dầu hoặc khí được chứa trong ống hoặc ống mềm, đo đạc chỉ có thể thực hiện tại những điểm kiểm tra được lắp sẵn như một phần của thiết kế gốc. Các điểm kiểm tra có thể được nối ống theo yêu cầu, nhưng có thể bị dẫn đến nguy cơ bị nhiễm bụi do cắt hoặc hàn ống, không khí lọc vào hệ thống thủy lực phải được xả bỏ hoàn toàn. Nhà thiết kế phải dự đoán các vị trí có thể xảy ra sự cố, và đưa ra các điểm kiểm tra cần thiết như một phần của thiết kế ban đầu.
Tìm sự cố
Được thực hiện một cách ngẫu nhiên và tùy ý sẽ đưa đến thay thế nhiều bộ phận, dù không có lí do chính đáng. Phương pháp này đôi khi có thể đạt kết quả (Khi từng bộ phận đều được thay thế) nhưng tốn nhiều thời gian, công sức, và chi phí. Trong nhiều trường hợp, kết quả có hại hơn là có lợi, thậm chí gây nhiễm bẩn hệ thống
Có 3 cấp độ bảo dưỡng
Cấp 1
Đưa thiết bị vận hành trở lại. Khi tìm được nguyên nhân sự cố, kỹ thuật viên lựa chọn phương pháp xử lý, sửa chữa hoặc thay thế toàn bộ cụm bị hỏng. Quyết định này dựa vào chi phí, thời gian, phụ tùng có sẵn, trình độ kỹ thuật, môi trường nhà máy, và chính sách của công ty.
Cấp 2
Sửa chữa toàn bộ cụm bị sự cố đã được nhóm kỹ thuật viên thứ nhất tháo ra và thay mới. Hoạt động này phải được thực hiện ở xưởng sạch sẽ và trang bị tốt, đây thường là nhóm công việc được quy định rõ trong sổ tay hướng dẫn do nhà chế tạo cung cấp.
Cấp 3
Trả thiết bị cần sửa chữa cho nhà chế tạo. Cấp độ này cần được xác định theo độ phức tạp của thiết bị, khả năng của nhân viên, chi phí, thời gian, và chế độ bao hành của nhà sản xuất.
Trong ba cấp độ này, cấp bảo dưỡng thứ nhất là vất vả nhất, vì phải xác định hư hỏng, áp lực lớn từ bộ phận sản xuất và trách nhiệm cao.
Viết bình luận của bạn